

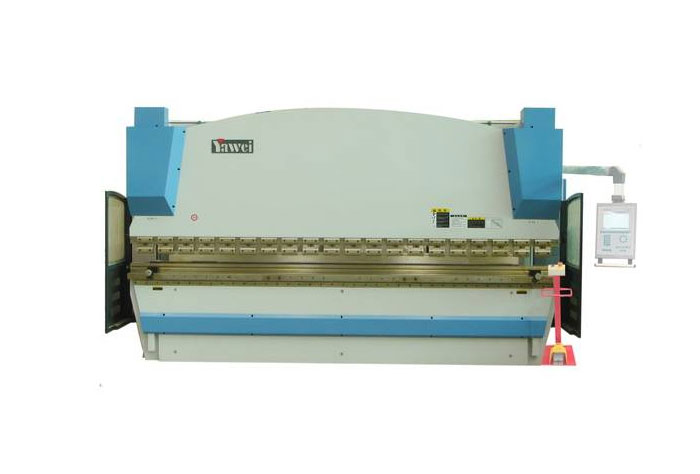
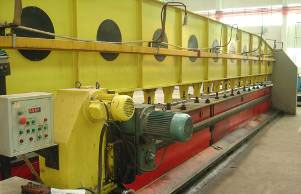
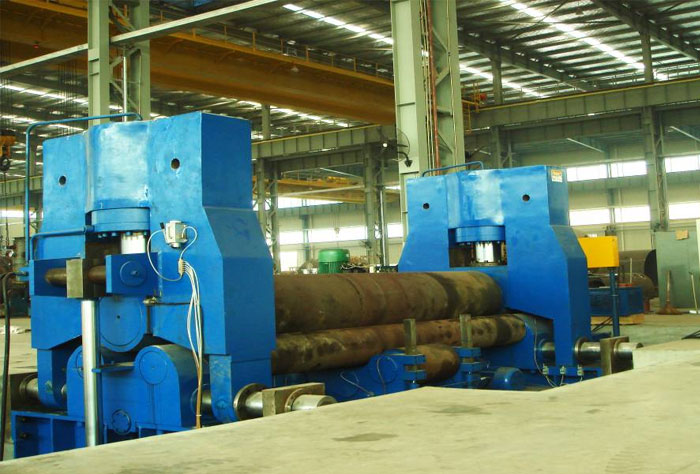
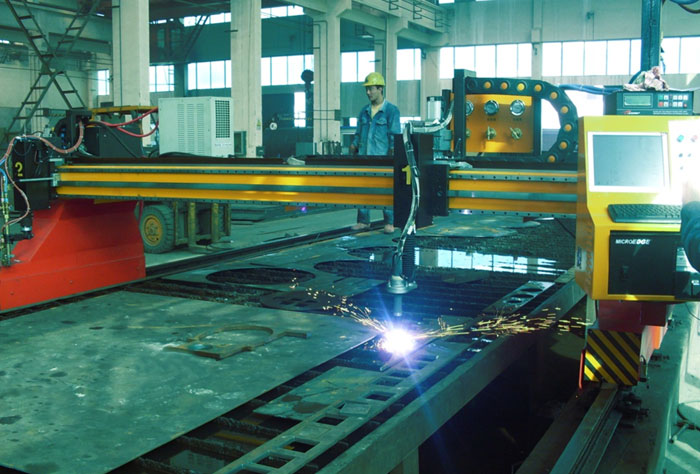
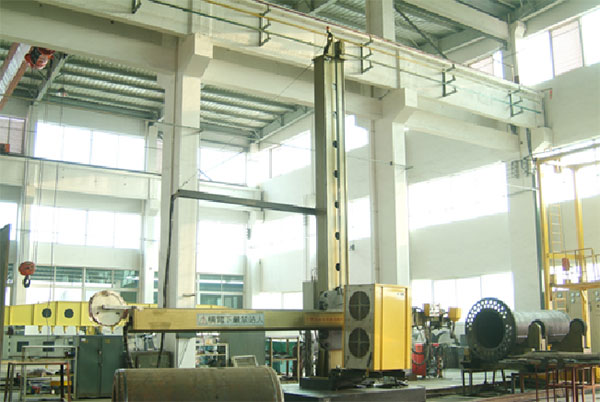
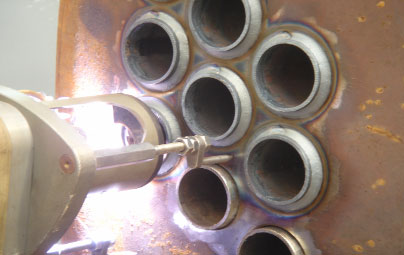
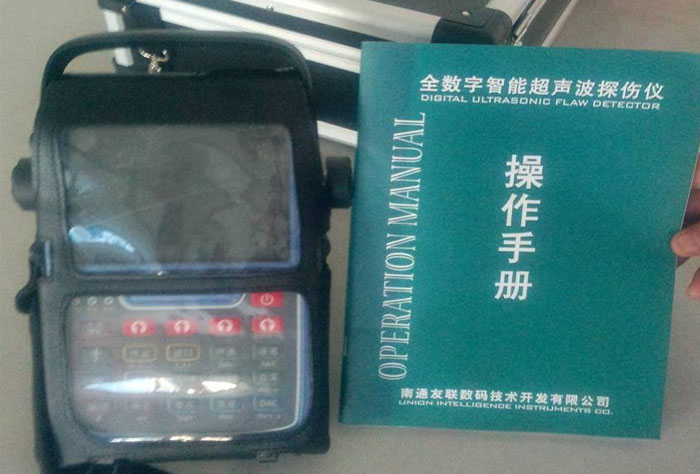

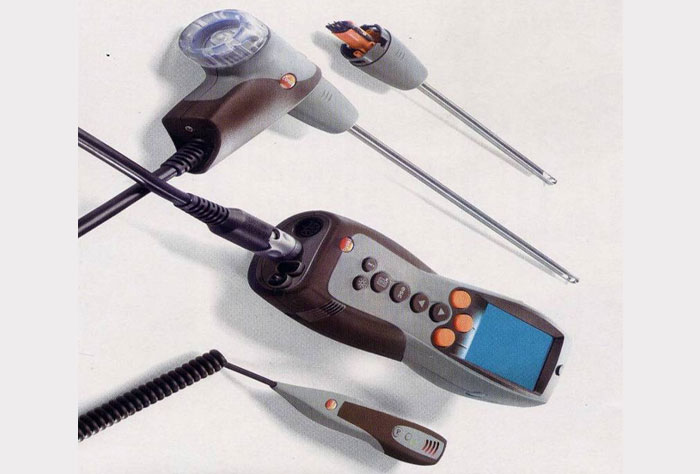

Mainly responsible for the design and development of Zhongrui boiler and boi"> ?
LOCATION : HOME > R & D Center
R & D Center
Sino-Swiss Boiler R&D Center is a provincial-level enterprise technology center
Committed to the R&D and innovation of boilers, carrying the mission of providing core technical support for Zhongrui Boiler to create an internationally renowned brand
Mainly responsible for the design and development of Zhongrui boiler and boi
After years of exploration and improvement, the technical center has formed a set of management system and operation mechanism suitable for Sino-Swiss characteristics, which has played a big role in the company's production and management and technological innovation. The technology center encourages technological innovation within the enterprise, protects technological innovation achievements, promotes the transformation and application of technological achievements, and encourages the enthusiasm of scientific and technological personnel for technological innovation, and plays an active role in ultimately improving the technological level and market competitiveness of enterprises. The Technology Center has joined hands with research institutes and institutions such as Xi'an Jiaotong University, Shanghai Industrial Boiler Research Institute, and Yangzhou University to combine research work with corporate applications, greatly improving the company's technological innovation capabilities.
equipment Exhibition
Zhongrui Boiler has established a complete set of product quality assurance system by introducing the most advanced production equipment and testing e
Seiko process
14 Seiko craftsmanship creates convenient and fast boilers for users
First process
Cutting
The blanking process is the pre-process of boiler manufacturing, and it is the key process to ensure the quality of boiler manufacturing. In this process, not only the accuracy of the blanking size but also the correctness of the blanking material must be ensured. The materials of the process must be materials that have passed the inspection according to the relevant regulations of the state and the enterprise. Before the material is cut, the materials should be sampled and transplanted and physical and chemical properties tested. The mark consists of a check mark and a color mark. This process tracks the use of all boards.
Second process
CNC cutting
Our company mainly adopts imported CNC flame (plasma) cutting machine, which can carry out 100% automatic CNC cutting and cutting of the board. The main advantages are:
1. The computer automatically programs to cut plates of any geometric shape;
2, cutting speed is fast;
3. High work efficiency;
4, the part size accuracy is high;
5, the use rate of sheet metal is high.
Third process
Groove processing
The beveling is done by the edge milling machine. Its main features are:
1. The maximum processing capacity of the equipment is 12 meters.
2, the board can be processed 0-45 degrees, to ensure the needs of various forms of welding groove.
3. The processing quality can reach a straightness error of less than 0.3mm/m, the total length of the straightness error is less than 1.5mm, and the surface finish reaches Ra6.3.
Fourth process
Volume
The rounding process is a basic process for the basic forming of the boiler. This process is mainly completed using the three-painted universal coiling machine industry. The main advantages are:
1. The maximum machinable plate thickness is 30mm, the maximum plate width is 2500mm, and the maximum diameter is 2600mm.
2, the processing range is large, the cone cylinder can be processed at the same time; 3, automatic programming, high work efficiency.
4. The steel plate does not need pre-bending, and the pre-bending quality and the consistency of the forming are high, which can ensure the assembly of the later group well.
Fifth process
Drilling reaming
Drilling and reaming: When processing the tube hole of each tube, our company first uses the method of cutting the hole with CNC cutting machine, and then using the radial drilling machine to ream the hole to improve the quality of the tube hole. The benefits of this method are:
1, no need to manually cross-line, the efficiency is increased by 3 times.
2. The processing deformation is small and the stress is low;
3. High cutting position and dimensional accuracy.
Sixth process
Group
Pairs: The group-to-process is mainly to combine the parts of the body of the body into a complete part.
Seventh process
Welding
Welding: Our company uses submerged arc automatic welding, argon arc welding and carbon dioxide gas shielded welding to test the circumferential, longitudinal and fillet welds formed between the pressure parts and the non-pressure parts. Main features of submerged arc automatic welding:
1. Fast welding speed and high production efficiency;
2, the weld quality is good, the appearance is beautiful;
3. The welding quality is stable;
4. Save welding materials and electrical energy.
Eighth process
NDT
Non-destructive testing: The quality of weld test welding will directly affect the safety of boiler operation. To this end, our company has specially set up the welding seam orientation and circumferential X-ray non-destructive testing process. The reliability and safety of the equipment are high, and the correctness of the welding quality inspection and evaluation is confirmed.
Ninth process
Mechanical properties test
Mechanical properties test: This process is mainly an important process for material re-inspection and mechanical property test of raw materials and product welding test pieces. It can be used for tensile and bending tests on the sheet to ensure the welding performance of the material and the materials used in the product. The materials are all up to the national standards.
The tenth process
Water pressure experiment
Water pressure test: The water pressure test is a heavy process for detecting the strength and tightness of the pressure-bearing components, and is also a key step for comprehensively testing the safety of the boiler operation. This process must be accepted by the Quality and Technical Supervision Bureau of the inspection of the stop point, the company's hydraulic pressure test once pass rate of 100%, to ensure that the use of Zhongrui boiler is absolutely safe.
The eleventh process
包裝工序
The packaging process is a process of laying the insulation material onto the shell and outsourcing the imported color plate. The carefully designed insulation structure of Zhongrui Boiler uses double-layer glass wool to greatly improve the thermal insulation performance, so that the temperature of the outer wall of the boiler furnace is much lower than the national design standard. Thereby effectively reducing the heat loss of the boiler and ensuring that the boiler has a higher thermal efficiency.
Twelfth process
Pipeline, electrical installation
Pipeline and electrical installation are a process in which the boiler is integrally formed. Our company takes the lead in integrating the programmable controller and the touch screen in the electrical control, and applies it to the operation control of the boiler. It can realize various modern control functions such as boiler automatic control, network group control, computer group control and remote control. State-of-the-art hardware and practical and secure software technology ensure full-automatic and high-quality production.
The thirteenth process
Thermal test
Thermal test: The thermal test procedure is a simulation performance test performed before the product is delivered. This process is also the most important process for our company to verify the final performance quality of the products. It is unique to China and Switzerland. This process ensures that the operating parameters of each boiler meet the design requirements, the use of boilers is more secure and reliable, and provides reliable parameter data for future boiler improvements.
The fourteenth process
Outer packaging
Outer packaging: The above process can be fully packaged before the boiler can be packaged. The outer packaging process includes plastic enamel and packaging to ensure the safety and appearance quality of the boiler during transportation.
Quality system
Commitment: Cherish every opportunity to serve customers, do a good job, do it again, make users satisfied, users are not satisfied, we must improve
Standard regulations
All regulations and standards that are activated and implemented by the company are current valid versions. The above excerpts may be replaced by new